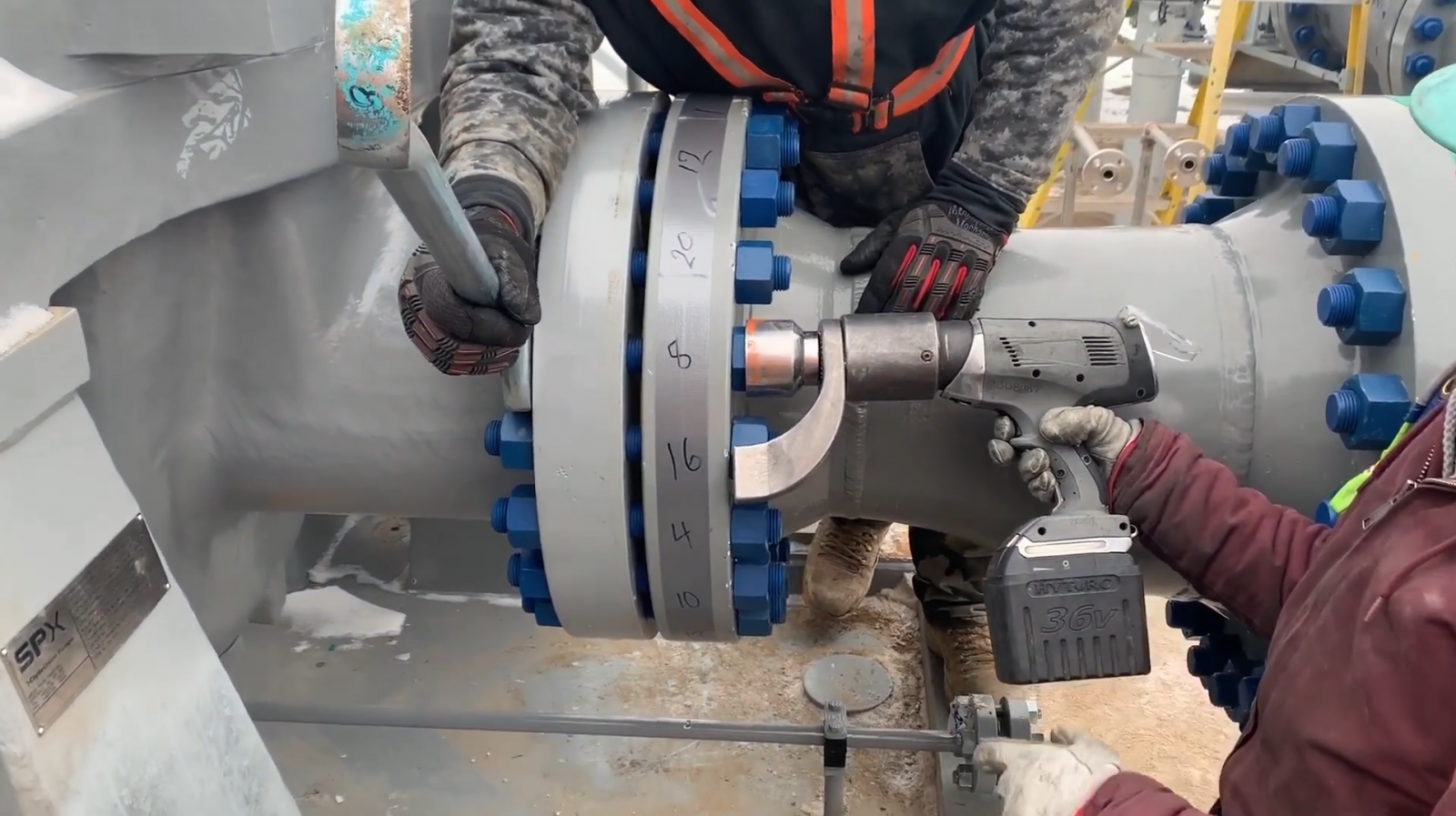
Five Things You Need to Implement a Precision Maintenance Program
Precision Maintenance can be used as a process improvement strategy. A strategy that will pay dividends. This process is easy to implement. In fact, you do most of the work already. The beauty of it all is that there is not a lot of cost involved and if you’re smart, you can implement the process on one machine at a time.
Precision maintenance is not new, it has been in our company name BENCHMARK PDM for many years. We chose the word BENCHMARK because it means a standard by which something can be measured from. The acronym PDM stands for precision driven maintenance. So, our goal has been and still is to set the standard for precision maintenance.
In simplistic terms, Precision Maintenance means working to a recognized standard tolerance or specification. Just doing that will improve you work processes and the pay off is a much improved and reliable machine (asset). It is important to note that when I say recognized, it means the standard is approved by an organization such as the Canadian Standards Association (CSA), the International Standards Association (ISO) or the American National Standards Institute (ANSI). There are many used in the industry, a common one is the ISO 10816 vibration standard tolerance chart (see image below).
Are there exceptions to using a recognized standard? Absolutely. There is the American Petroleum Institute API686 and while only a guideline and not a standard, this document was the go-to bible for anyone doing pump installations and still is.
When implementing Precision Maintenance there are five things that you should already have or need to have to be successful.
- Work Procedures
Work procedures are written documents that follow the work process. You have them as part of your Preventive maintenance program. But do you have them for a pump overhaul? The procedure should include the standard tolerances and specifications you would need doing the work. What this would give you is consistency. If you do not have written procedures or old outdated ones, the best people to write them are the tradesmen as they know the work process the best. Better still, do it as a team building exercise as it creates buy in. However, they must be clear, no ambiguity, all must understand and be on the same page.
- Measuring Tools
Precision Maintenance requires exact measurement. Obviously, you need instruments that can achieve this. The actual recommendation is to use instruments that can measure under the tolerance you require. The tighter the tolerance the better the result but you cannot have a tolerance that you cannot measure. This means you need the right tools for the job. Always try to use digital so that the measured value or result is saved electronically. It is a known fact that when using instruments such as theodolites, dial gauges or levels for example, the greatest error occurs during the transfer of the seen value. My one piece of advice is do not buy junk. You need something that the team will use. Get them involved in choosing the tools required.
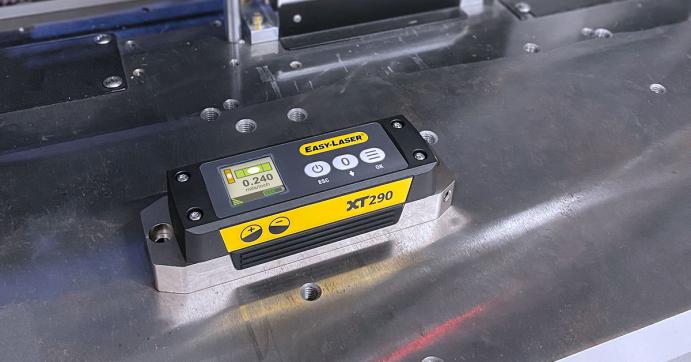
Easy-Laser XT290 Digital Precision Level
- Data processing system
This is so important because it gives you an organized structure. You probably have a PM program, which of course is a must, that is controlled by a CMMS/EAM system. In it you will have planned work orders, back log orders, PM schedules, CBM tasks, etc.
Depending on the capabilities of you CMMS/EAM you should have an individual file for all the plants assets. In each one should be a benchmark record of the machines normal operating condition. For example, the normal operation temperature should be known and where you would take those measurements to verify this. Simple enough to do but so helpful for the PM tech. There should also be an asset history file.
And this is where we often see the breakdown in the system. There may be a file but what is missing from many is the asset/machines installation report or a coming into service report. This is the information that controls the reliability of this machine. Imagine if you had to do a breakdown analysis after a failure and did not have this information? You would be relying on guess work or maybe wrong information.
A Precision Maintenance program guarantees that you have this file because a precision machine installation has mechanical measured items such as these below.
- Base flatness and level
- Shaft runout
- Coupling runout
- Pipe and conduit strain
- Soft foot
- Offline To Running (OLTR) machinery movement
- Shaft centerline to shaft centerline (alignment)
All of these items and the recognized standard tolerances/specs can be found in ANSI/ASA S2.75-2017/Part 1. With an installation report and a commissioning report it guarantees the machine has a good starting point when starting service. And throughout its life there will be added work to this report such as an As Found and an As Left alignments, or a base flatness change as things do move over time.
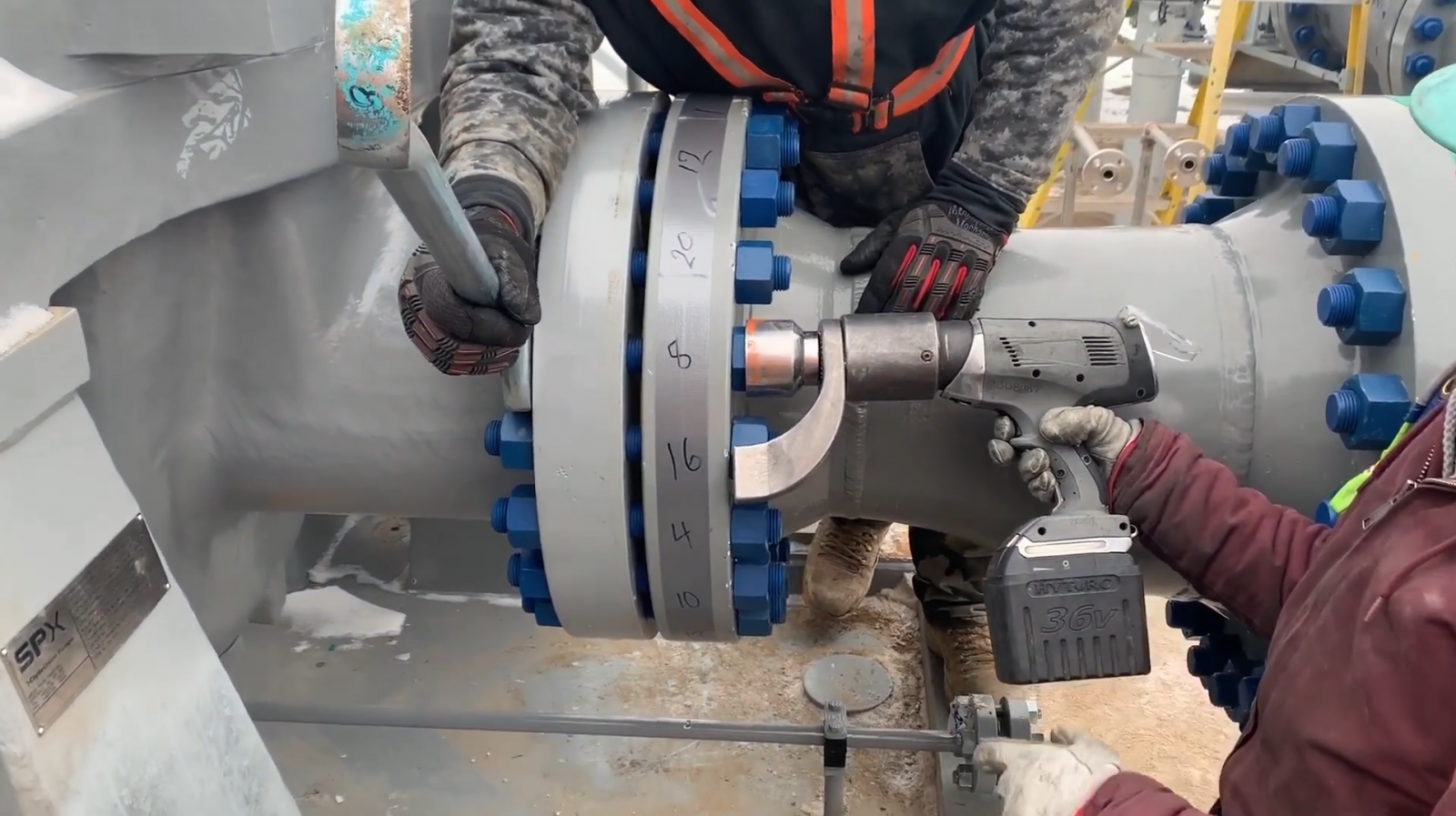
Tightening the pipe flange bolts and not pictured is an Easy-Laser XT770 laser alignment system checking for pipe strain live time (Photo credit: Brian Franks – https://jettechmechanical.com/).
- The right skill sets for the work
I had a conversation with a maintenance shop foreman who suggested that not everyone in the shop had the same sized toolbox and that he would pick and choose who to put on what job. What he meant was that not everyone has the same skill sets. For example, I know a company who bought an expensive and not so user-friendly laser alignment system. The problem is that not all the shop guys can use it. It may be taken to the job site but unfortunately not used correctly or not used at all. This is one of the reasons we are developing training videos to help support some tradesmen who struggle with new technology. They can take their time and review it as often as they like especially before going out to do and alignment job. With Precision Maintenance all should be proficient in taking and recording measurements. So, you may want to invest in training.
- The right team culture
I first heard the term Precision Maintenance from Ralph Buscarello of Update international who is the gentleman that taught me shaft alignment using dial indicators almost 40 years ago. I have heard others promoting this as the next big thing. But the reality is that it has been with us for a long time. Some companies, not a lot, do it, others do it but not as successful.
If you are in maintenance, whether in management or skilled trades, embarking on such a program as this is challenging. It is a very worthwhile program, but it is a big commitment to do it and stay with it. The overall benefits are large in the form of machine/asset reliability. A side benefit is that you have to do this together as a group, dare I even say team, which does put some people off. However, there are different cultures that produce different teams. You may want to hug every morning before starting work but others wont. In today’s industrial environment it should be evident to all that we have to work together in order to compete. So, my advice is that you sit down collectively and ask some tough questions such as can we do this and what do we need?
In today’s world of covid we use scientific knowledge to help us make choices or decisions about our health. That’s not unlike what you do with your Condition Based maintenance program where decisions are based on the measurement/data that is taken. It is the same with this program. It is data driven. Quantifiable, reproducible measurements are taken, analysed and compared to a standard. Decision and or actions are taken and the whole process is documented. For well over ten years our training has been called MAAD which is an acronym for Measure, Analyse, Act and Document. I would suggest that you do something along the same lines as this if you want to improve your maintenance process. And quite simply do the job right. You’re doing the work already.
By John Lambert
You can also find a version of this article in MRO Magazine’s June 2021 Digital Edition here.
0 comments
Write a comment