What is Shaft Alignment?
While “shaft alignment” is the common term, the correct term would be “shaft to shaft alignment”. However, when we say shaft alignment, it is assumed that we are aligning one shaft to another. What we’re trying to accomplish is the alignment of the rotational center line of one shaft with the other shafts rotational center line. These shafts are usually being held in position by bearings attached to machines such as a pump and motor.
The goal is for these shafts to stay aligned when in operation, at full operating temperature and under load. The sheer torque of running machines will create an offset and angular misalignment, usually a combination of both (see Figure 1).
Many use the term “coupling alignment” which is incorrect. This was an old term used to describe the straightedge and feeler gauge method of alignment. This was normally done without shaft rotation. This method of alignment can still be used as a rough-in process prior to precision alignment, but it cannot achieve the necessary tolerances needed for modern day machines.
Wikipedia describes shaft alignment as “the process of aligning two or more shafts with each other to within a tolerated margin. It is an absolute requirement for machinery before the machinery is put in service.”
Remember – shaft alignment is only one aspect in the machinery installation process!
Rotating Machines and Shaft Alignment Applications
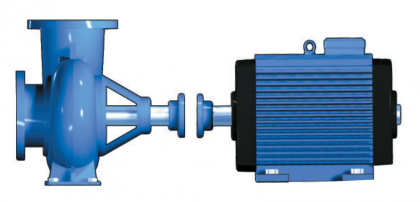
Figure 2
Rotating machines are usually described according to how they are connected to each other. The most common are horizontally mounted machines, usually a pump and motor (see Figure 2). Rotating machines can also be positioned vertically on a flange-mount in some circumstances.
Another type is offset mounted, or cardan-shaft-coupled machines aka universal joints. These often have some type of drive, for example rollers in a papermaking machine. Many people wrongly believe that cardan-shaft-coupled machines do not need to be aligned as accurately. But an angular error in these machines causes a non-linear motion, which causes forces and vibrations in bearings, couplings and seals. In other words, shortens the service life.
Often several machines are connected in line, usually called a Machine Train, for example a gearbox between engine and the driven machine.
A modern shaft alignment system can measure all the above types of machine.
Why is Shaft Alignment Important?
Correctly aligned shafts mean many improvements:
- Increased availability and productivity of the machine = assured production.
- Increased service life of bearings and seals = fewer removal of replacement parts
- Complete seals = less leakage and better working environment
- Optimally utilised lubricant film = less risk of overheating and secondary damage
- Reduced lubricant leakage = less lubricant consumption
- Less vibration = reduced noise level
- Less risk of serious breakdowns = safer working environment
Greater overall savings with fewer spare parts, lower energy consumption and less unscheduled downtime.
Shaft Alignment: Laser technology vs. Dials
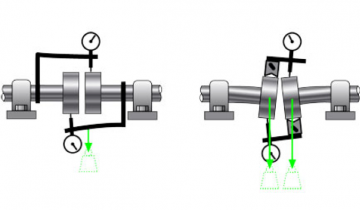
Figure 3
Using a laser-based shaft alignment system is without doubt the best method. Yes, you can use a dial indicator system, however, these systems are fraught with errors. For example:
- Dial alignment takes longer.
- Requires experience/knowledge.
- Calculations are needed
- Dial alignment kits are prone to mounting errors and looseness.
- Dial sag has to be measured and compensated for (see Figure 3).
- Dial sets can not produce documented results of before and after alignment work.
The biggest issue is the human element. This means the transfer of information from what is read on the dial is many times input incorrectly into the calculation.
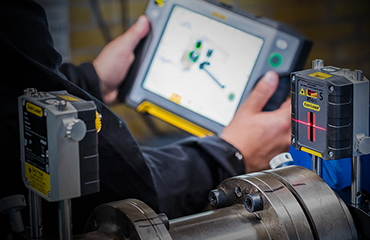
Figure 4
Laser alignment tools (see Figure 4) on the other hand are considerably easier and faster to use (although speed is not an essential factor – repeatable measurements and precise results are the goals). Laser alignment systems also:
- covers many more applications such as Horizontal, Vertical, Spacer shafts, Cardan shaft (universal jointed shaft), etc.
- spans large distances (ie. jackshafts). A basic system will span 3 meters while a professional system will span 20 meters
- have built-in tolerance guidelines including the new ANSI standard.
- takes measurements with as little as 40 degrees of shaft rotation
- can compensate for offsets because of sleeve bearings or thermal growth issues.
Most importantly they can give a documented, detailed report of the installation (see Easy-Laser XT Report example in Figure 5). Because if you have to do a breakdown analysis on this machine and you don’t have this report you will only be guessing as to what was done. For motor shaft alignment tools & equipment contact us.
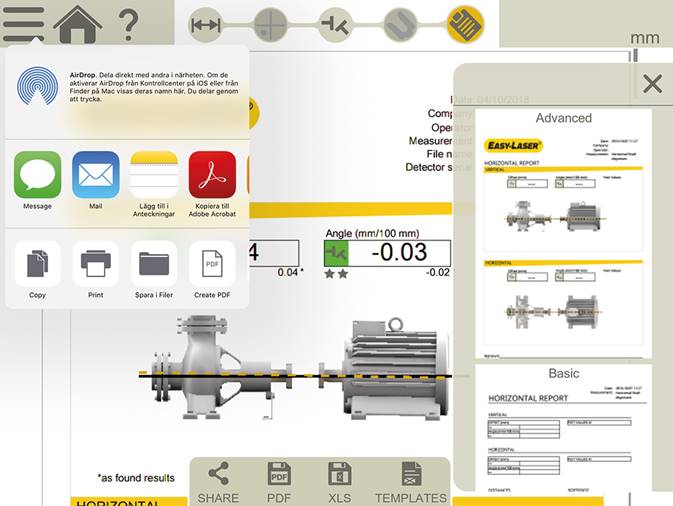
Figure 5
We are Canada’s Master Easy-Laser Distributor
Shaft Alignment Resources
Laser Shaft Alignment Videos