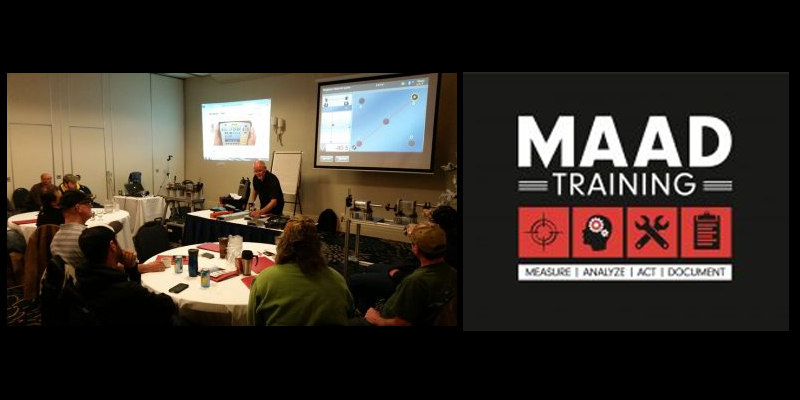
Get MAAD about Maintenance!
How getting a little MAAD can help you with your Maintenance Processes
Most of us have heard enough about Reactive, Preventive, and Predictive Maintenance practices. Well how about Insane Maintenance? Yes that’s right, Insane Maintenance. You see, a definition of insanity is “to do the same thing over and over and to expect a different result”. If you think about it, do we – in the maintenance world – repair equipment only to have it breakdown again and again? How many bearings will be replaced this year in say an industrial area such as Fort McMurray Alberta – the center of Canada’s oil? Or say Sarnia Ontario, known as the chemical valley? To be honest, I don’t know but an educated guess would be in the millions.
This can be surprising to some because it is said that a bearings life is infinite as long as you can keep lubricant between the ball and the race. Belts, sheaves, chains, and sprockets have a life span so we expect to replace them. However, most do not reach their full life expectancy. Bearings, on the other hand, should last a long, long time – but they don’t. The reason they don’t is because of the static and dynamic stress that they have to operate under.
This is the first of many articles that will be published through our newsletter and website that we hope will be of interest to you and will help you find the causes of these stresses. We will also provide some simple condition monitoring tips to help you through your maintenance processes. You see, in order to stop doing the same thing over and over we have to change the process. Sort of like trying to lose weight; it’s a lifestyle change one has to make. Some call it Precision Maintenance but it basically means “Doing the job right and to a tolerance”. Yes, you will have to get better at break-down analysis but hopefully not as many times as before.
Now I don’t think maintenance is anything one should be crazy about but I would like to suggest that you get MAAD about it. MAAD stands for Measure, Analyze, Action and Document. This is something you should be doing throughout your condition monitoring program and when you are installing a machine. Actually, you can do this for any measurement that is important to you. We have gone as far as changing the name of our training program to MAAD (see below our first MAAD Training session on the road in Timmins, ON) as well as our brand new to MAAD Maintenance newsletter (click here to subscribe).
The following is an example of how we would use the MAAD process to do a shaft to shaft alignment. Now normally on a machine installation we would start with base measurements but for now we will focus briefly on the shafts just to give you the idea of the MAAD process.
Measurement. What’s important? Obviously accuracy for one. This means it has to be quantifiable (a known measure) seen by all. It also has to be repeatable. We all know about “measure twice and cut once.” Well it’s the same in this case. If the results are not repeatable you don’t have a good measurement. And why stop at two? There is nothing wrong with taking three readings to make sure that you have correct results. Repeatability is very important and this reading should be recorded as an “as found” (AF) result. Remember, to control a process you have to measure something but is has to be accurate and repeatable.
Analyze. The analysis section starts when you have the AF result, it’s seeing what you have and planning the optimum move for machine units. You may look at previous documentation (the machines history), temperature readings for thermal growth considerations, vibration data and so on. You ask the question, can the correction be done? Do we have the means? And of course the answer may be simple that yes you’re good to go.
Action. Now you should have a plan and the action is to implement that plan. Even if it’s to do nothing, that in itself is an action. However, if you are moving the machine, it has to be a controlled move using jacking bolts – not hitting the machine with a mallet (or something worse). Now let’s say you come up with a problem such as being bolt-bound, which may mean you have to go back to the Analysis stage. If you are using dials to align, you may have to graph it to see your options or if you are using a laser, you can use the bolt/base bound options to get around the problem.
Documentation, if done right, has been going on through the whole process. This is a very valuable record that should be added to the machines history. Why is it valuable? Well because in order to move forward it is said we must look at our history. Which means to improve your maintenance process you need to look at the documented data in the machines history file.
About Author
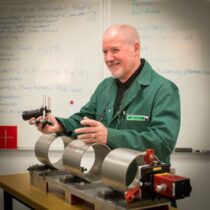
0 comments
Write a comment