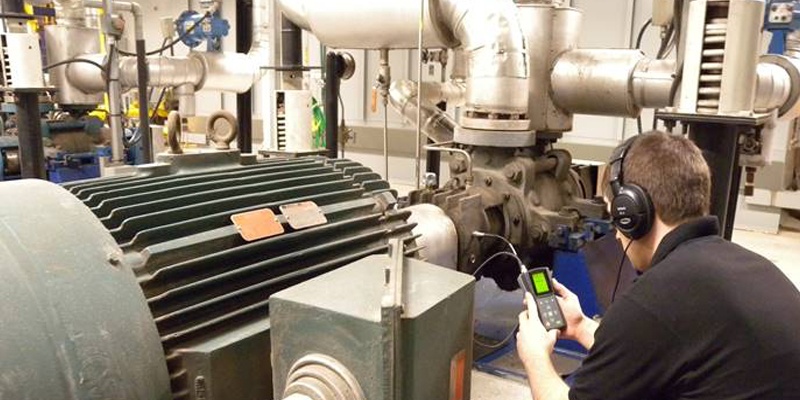
Le but ultime de toute personne travaillant dans le domaine de la maintenance industrielle devrait être d’obtenir la durée de vie optimale et complète de nos machines. Pour ce faire, nous devons modifier nos processus de maintenance actuels ou, du moins, la façon dont beaucoup d’usines font les choses. Je vois que beaucoup d’entreprises ont une variante d’un programme de maintenance basé sur l’état des machines, mais se demandent pourquoi elles ont encore des pannes de machines. Elles n’ont pas tort de procéder à une maintenance basée sur l’état des machines, mais cela ne suffira pas à empêcher vos machines de tomber en panne. Tout d’abord, laissez-moi vous expliquer pourquoi la maintenance conditionnelle fonctionne.
Le principe de la maintenance conditionnelle est que la plupart des pannes donnent un avertissement sur le fait qu’elles sont sur le point de se produire.
L’intervalle P à F
Cet avertissement est appelé défaillance potentielle et est défini comme un état physique identifiable qui indique qu’une défaillance fonctionnelle est sur le point de se produire ou est en train de se produire.
La défaillance fonctionnelle est définie comme l’incapacité d’un article à satisfaire à une norme de performance spécifiée. L’intervalle P à F est une illustration bien connue (voir la figure 1 ci-dessous).
Il existe de nombreuses techniques différentes pour mesurer et détecter les défaillances potentielles. Vous choisissez ce qui est le mieux pour vous et votre machine. Par exemple, si vous aviez une boîte de vitesses à rotation lente, vous pouvez utiliser l’analyse de l’huile. Les instruments les plus populaires pour mesurer les défaillances potentielles sont les vibrations, les ultrasons, l’analyse de l’huile et la température, mais il y en a d’autres.
Plus vite une défaillance potentielle est détectée, plus l’intervalle P-F peut être long. Des intervalles P-F plus longs signifient que les inspections doivent être effectuées moins souvent et, plus important encore, que l’on dispose de plus de temps pour prendre les mesures nécessaires afin d’éviter les conséquences de la défaillance.
Ce type de maintenance conditionnelle ou de surveillance conditionnelle fonctionne-t-il ?
Oui, car vous pouvez éviter les temps d’arrêt et peut-être économiser de l’argent.
Les pannes nous arrivent de plusieurs façons et nous avons évidemment de nombreux moyens de les combattre. Si vous détectez la panne potentielle suffisamment tôt (et cela peut prendre des mois et des mois avant la panne réelle), cela signifie que vous pouvez éviter la panne. Vous pouvez programmer une panne pour effectuer une réparation ou un entretien. Il ne s’agit pas d’une panne, la machine ne s’est pas arrêtée, ce n’est pas un temps d’arrêt. Il s’agit d’éviter des coûts et l’usine peut économiser sur la perte de production interrompue à cause des coûts d’arrêt. Évitez les temps d’arrêt, contrôlez la panne, planifiez les travaux de maintenance. C’est une victoire.
Pensez aux dommages secondaires. Le joint d’étanchéité peut aller dans une boîte de vitesses et son remplacement coûte 1 000 dollars (les coûts sont des suppositions, pour des raisons de commodité). Si vous ne l’attrapez pas et que le roulement est contaminé, cela devient une révision de la boîte de vitesses pour disons 5 000 $. Mais si le roulement se bloque sur un arbre, il faut alors remplacer l’arbre et peut-être plus.
Le coût des dommages secondaires peut être énorme, alors oui, la surveillance des conditions de fonctionnement fonctionne et est bien faite, elle vous fait gagner beaucoup de temps et d’argent. Mais il y a un problème avec la maintenance conditionnelle et c’est la même chose pour la maintenance prédictive. Nous avons toujours des pannes de machines.
L’analyse des causes profondes et l’élimination des défauts sont indispensables
Une définition de la folie est de faire la même chose encore et encore et d’attendre un résultat différent. Si nous continuons à remplacer les roulements sans trouver la cause de la défaillance, nous sommes fous n’est-ce pas ?
Sommes-nous coupables de ne faire que réparer l’effet et de ne pas trouver la cause ? Se contenter de réparer le défaut/l’effet, c’est de la maintenance réactive. Un programme de maintenance conditionnelle ou tout autre programme nécessite un processus d’élimination des défauts.
Il s’agit généralement d’une analyse de la cause première, c’est-à-dire du processus de définition, de compréhension et de résolution d’un problème.
Ce diagramme en arête de poisson (voir figure 2) est un outil de base utilisé dans l’analyse des causes profondes. Il y a quelques années, on l’appelait analyse de défaillance. Nous savons que l'”effet” est que la machine est en panne, mais quelle est la véritable “cause” de la panne.
Le processus a consisté à mettre en place une équipe interfonctionnelle afin de pouvoir réfléchir à la cause de l’échec. C’est une bonne idée, mais vous devez vous assurer que vous avez des personnes qui ont une connaissance directe du processus examiné. Pas seulement des personnes qui représentent un service. Ensuite, nous avons eu un processus étape par étape à creuser pour trouver la véritable cause de l’échec.
Mais ce n’était qu’un des outils que nous avons utilisés, nous avons aussi utilisé la méthode des “5 raisons” qui était ma préférée. Il s’agit simplement de se poser la question du pourquoi suffisamment de fois pour s’attaquer à la cause profonde du problème. Bien sûr, vous ne devez pas vous limiter à poser seulement 5 questions, vous en posez autant que nécessaire.
Ce ne sont là que deux des outils disponibles. Il en existe d’autres, comme l’analyse des modes de défaillance et de leurs effets (AMDE). Quel que soit l’outil que vous utilisez, le fait est que vous devez éliminer les défauts dans le cadre de vos processus de maintenance.
L’élimination des défauts est la suppression de la cause, ce qui vous permettra de prolonger la durée de vie de vos machines. L’idée est de s’assurer que “vous réparez pour toujours, plutôt que de réparer pour toujours”. Ainsi, lorsque quelque chose tombe en panne, vous vous assurez qu’elle ne se reproduira pas avec le temps, vous réduisez le nombre de pannes et augmentez votre temps de fonctionnement.
Après avoir éliminé les défauts, que vous soyez en train de réviser, de réparer ou de reconcevoir, vous réinstallez la machine. Pour cela, vous devez mettre en œuvre des compétences et des techniques de maintenance de précision.
Maintenance de précision
La maintenance de précision est simple, elle signifie travailler selon une norme reconnue. Un ensemble de tolérances sur lesquelles vous et votre équipe vous entendez. Plus la tolérance est stricte, meilleur est le résultat. Mais vous ne pouvez pas avoir une tolérance que vous ne pouvez pas mesurer.
La maintenance de précision signifie “améliorer les compétences” de votre personnel. Pour cela, il faut disposer des bons outils, mais aussi de la bonne formation. Ses normes d’acceptation des machines, l’équilibrage de précision, l’alignement, les normes de planéité de la base, la suppression des contraintes sur les machines et bien plus encore. Voir les figures 3 et 4 pour quelques exemples.
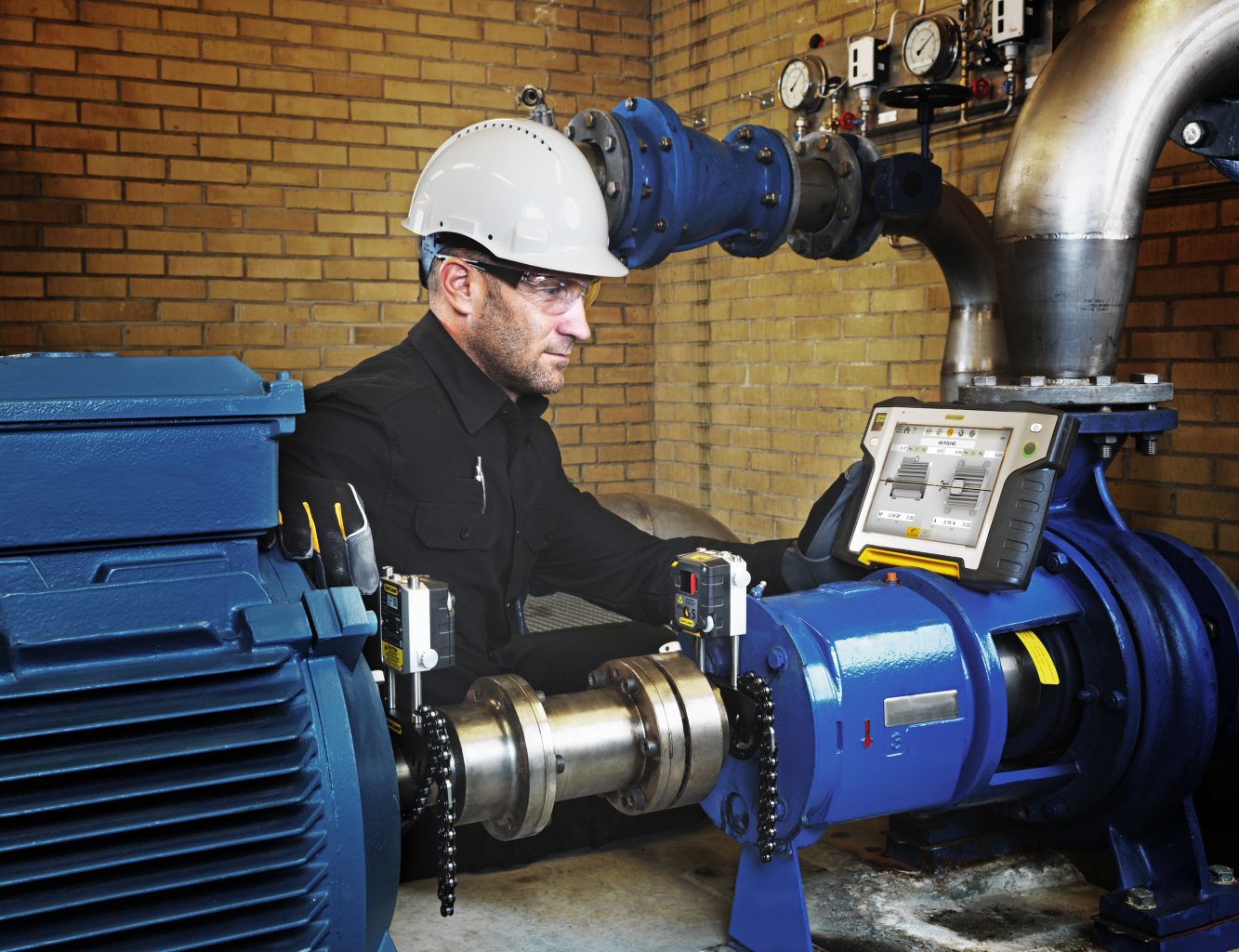
Figure 3 – Alignement d’arbre à l’aide du système Easy-Laser XT770.
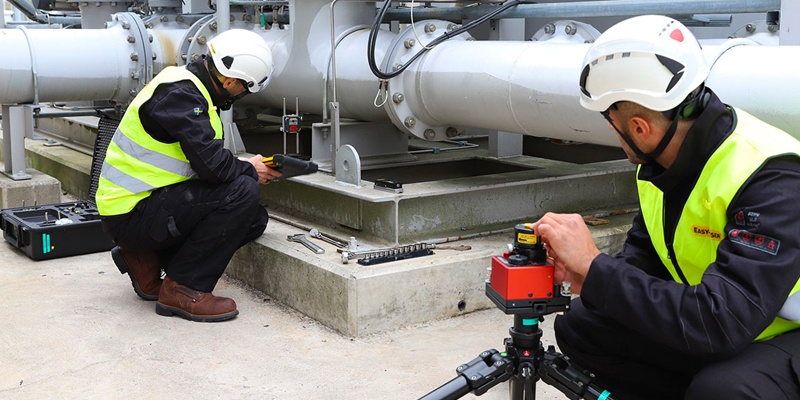
Figure 4 – Mesure de précision de la planéité de la base à l’aide du système Easy-Laser XT770 GEO
Le plus important – c’est la mise en place d’une norme et la documentation du processus.
La réponse à la question de savoir pourquoi cela a été demandé dans l’analyse des causes profondes ci-dessus se trouve généralement dans la maintenance de précision.
Facteurs de contrôle dans la vie d’une machine
- Conception/Reconception
La conception d’une machine peut avoir un effet sur sa durée de vie. Cependant, en matière de maintenance, nous devons très souvent vivre avec la conception qui nous a été donnée. Disons qu’il s’agit d’une pompe qui a été sous-conçue pour l’application ; cela voudrait dire que la pompe commencerait sa vie dans un état de défaillance fonctionnelle parce qu’elle ne répond pas aux exigences. Il est donc évident que la conception doit être bien faite, sinon l’inévitable reconception est faite. Une révision de la conception des machines devrait être une nécessité dans toute analyse de défaillance.
- Révision/réparation
Les machines sont révisées (ou réparées généralement en cours de route) de nombreuses fois au cours de leur vie. Il est extrêmement important que cela soit fait correctement. De nombreuses entreprises sous-traitent ces travaux parce qu’elles ne disposent pas des installations (c’est-à-dire des salles blanches) nécessaires pour les effectuer correctement, car l’un des principaux problèmes lors de la révision est la contamination. Lorsqu’une machine est révisée, l’aspect le plus important est que les spécifications OEM pour l’ajustement des machines soient respectées. L’objectif est de la rendre à nouveau neuve.
- Installation
L’installation est la clé. C’est la chose la plus critique pour toutes les machines. Une machine bien conçue ou une machine bien révisée peut être ruinée par de mauvaises pratiques d’installation. L’installation doit être faite selon une norme telle que la norme ANSI/ASA S2.75-2017/Part 1 ou la spécification OEM si elle est meilleure.
- Mise en service
La mise en service est en fait une continuation de l’installation. En fait, elle devrait commencer par l’examen de la documentation de l’installation. Je pense que cela devrait être fait par un autre groupe que celui qui a fait l’installation, comme le groupe de fiabilité, par exemple. Chaque machine est différente, nous ne pouvons donc pas publier une liste de ce qu’il faut faire, mais toutes les procédures de fonctionnement des équipementiers doivent être suivies. Lorsque vous appuyez sur le bouton pour démarrer la machine, c’est là que vous devez prendre les mesures de la dilatation thermique (de l’arrêt au fonctionnement) afin que nous sachions si une correction est nécessaire avant de mettre la machine en service.
Lorsque la machine est en ligne, différents paramètres doivent être mesurés, tels que la température, le son et les vibrations, dans le cadre de votre programme de maintenance conditionnelle. Ces mesures sont les points de référence que vous utiliserez pour comparer les nouvelles mesures que vous prendrez tout au long de la vie de la machine. Tout changement par rapport à ces résultats signifie que la machine se détériore. Cependant, si vous avez fait un bon travail pour comprendre les causes profondes et utiliser les techniques de maintenance de précision dans les domaines que vous pouvez contrôler, cela devrait être dû au fait que la machine est usée et a eu une bonne durée de vie.
You can also find this article in the February 2020 digital edition of MRO Magazine here .